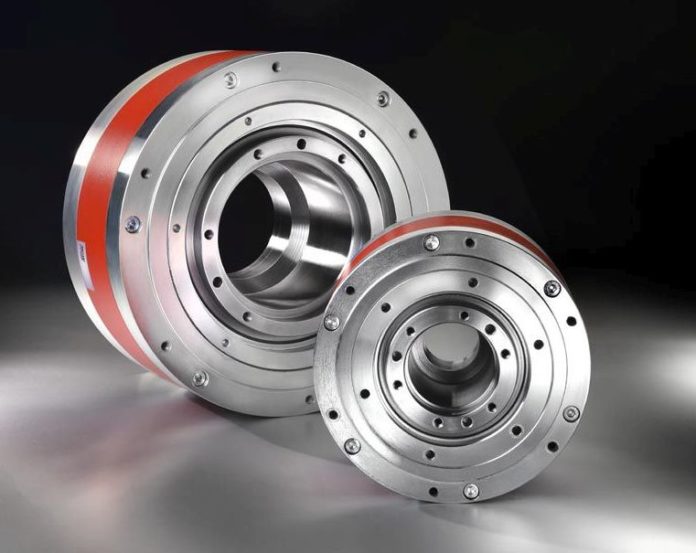
If you’re looking for flexibility, fewer parts and reduced assembly time, then you might want to consider incorporating frameless motors into your design. As the name suggests, a frameless motor consists of just the rotor-and-stator subcomponents. Unlike a brush motor, these components aren’t fixed into a motor housing or frame. Instead, in frameless motor systems, the design engineer must integrate the stator and rotor directly onto the machine assembly.
Regular servo applications use pulleys, gear heads, rotating nuts and bolt systems which in one way or another link to a mechanism or machine. Frameless motors are a way of replacing these electromechanical systems with fewer components with a direct drive capability.
So Why is Frameless Motor Technology Needed?
To generate cleaner mechanical assemblies which are also cost-efficient systems, you must take advantage of frameless motor technology. Servo performance is significantly improved due to reduced loss motion, backlash and the losses in motion control associated with gear trains.
Many applications require a compact footprint, reduced weight, and increased strength. Traditionally, space and weight considerations have always been an area where improvements have been needed, and frameless motors are a great solution. Because of the lack of moving parts and the lighter load, businesses usually realize improved energy consumption, which means cheaper operating costs.
Because geared motors have a lower torque to inertia ratio, they need to provide high torque to accelerate the motor. For direct drive torque motors, inertia is low, which makes them perfect for high speed, acceleration applications with instantaneous starting and stopping.
A frameless motor is usually designed to provide excellent torque density.
These motors come in all manner of shapes and sizes. In reality, their capabilities are only limited by the design engineer and the concepts he can imagine. However, in the future, VR technology will significantly improve this process, but more on that later on!
Currently, they are utilized in several applications throughout varying industries, including robots, surgical equipment, manufacturing automation, machine tools, and unmanned autonomous vehicles.
The versatility of frameless motors makes them excellent candidates for special purpose projects.
Other Reasons to Consider a Frameless Design
- Improved OEE by increased machine life and reduced maintenance.
- Smoother production flow with stable machine operation, improved balance, along with faster move and settle times
- Quieter and smoother machine operation as clunky mechanical components are removed from the system.
Things to Consider
Frameless motors offer plenty of advantages. They have no brushes, no gearboxes, worm gear drives or other transmission systems. Resulting in increased product lifespans and reliability while also reducing overall system costs.
On the flip side, they will have increased design time and need application-specific engineering, which can increase overall costs.
That means a cost-benefit analysis will need to be carried out for your project, and usually, frameless motors have proved better suited to applications that have a high production quantity or one-off special projects where cost isn’t the deciding factor.
Additionally, your technical requirements are fundamental when choosing a frameless motor for your project. You will need to determine your torque density requirements and energy consumption, but also understand the form factor available for your motion elements.
Most importantly, you will have to consider factors like size, weight and working envelope – the space in which the motor and machine will need to operate.
Your motor must be low clogging which will mean a smooth rotation and silent operation. You may even wish to consider fault monitoring and protection systems which are designed to shut down operations to protect the asset. You can review our catalog here and choose your specifications.
What Does the Future Hold for Frameless Motor Technology?
Just like most modern technologies, the trend is toward a smaller size. Designers are continually thinking up new ways to exploit the technology.
Frameless motors are incredibly accurate. In the machine tool environment, automated applications will require larger bandwidth capability to afford a higher degree of accuracy and control.
As humankind ventures deeper into space and eventually discovers the more inaccessible areas of our planet, this technology will become particularly useful. Extreme environments will require significant improvements in hardware. These types of motors will need to withstand extreme temperatures and pressures.
For example, frameless motors are already being used in oil and gas drilling applications as well as autonomous deep-sea submersibles which can reach depths of 4000m and beyond.
The advent of virtual reality will improve product designs and manufacturing, as well as the operation of these autonomous vehicles.
SRI International is developing the Taurus, a robot that can be used in bomb disposal or perform surgery using virtual reality headsets.
With a VR headset, the operator can see precisely what the robot sees. Inside the virtual environment, there’s also an interactive display with vital information, like a patient’s vital signs and fault/diagnostic readings.
By operating hand controls and foot pedals, it’s easy to maneuver the Taurus and use its tools and instruments. The Taurus is a brilliant example of how frameless motors and VR can be utilized together to perform critical tasks in environments deemed inhospitable or dangerous to humans.
Another example is from the defense Advanced Research Projects Agency or DARPA. The agency holds the DARPA Robotics Challenge, and the goal set for last year was to produce autonomous disaster relief humanoids. These devices shall be sent into arduous environments where life would typically be at risk. Not only will these devices aid rescuers, but they shall also lead the rescue or clean-up efforts in the absence of human oversight.
The Fukushima nuclear disaster as with the explosion at the Chernobyl power plant in Ukraine provides particularly strong examples of why robots with frameless motors are necessary. These types of incidents expose rescuers to lethal amounts of radiation which consequently makes the whole clean-up operation long and tedious and extremely dangerous.
Finally, the idea of being able to closely integrate frameless motor technology into gear, transmission, feedback and brake systems is precisely what most designers are striving for in their own applications.