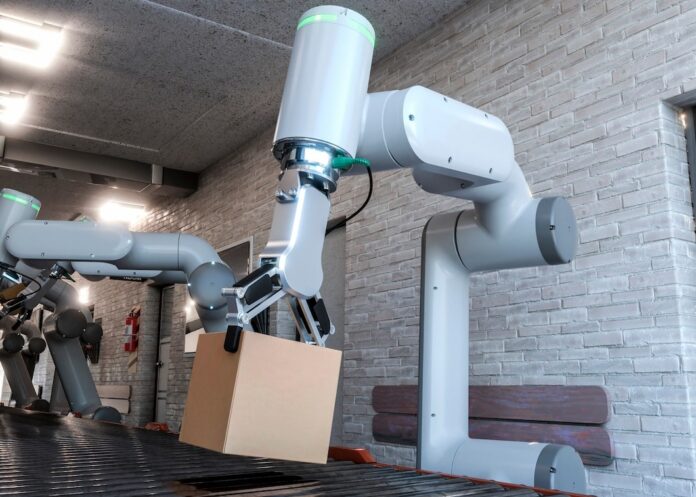
From assembling delicate electronics to constructing safety-critical aerospace components, the margin for error has shrunk to almost nothing. To meet these rigorous standards, the manufacturing industry increasingly relies on robotic precision.
Modern robotics, equipped with advanced sensors, grippers, and AI, allow manufacturers to complete intricate tasks with extraordinary accuracy.
Technological Innovations Driving Robotic Precision
Today’s robots leverage a combination of advanced technologies to achieve a high degree of precision. Let’s look at some of the most impactful innovations that make robotic accuracy possible in complex tasks.
Sensors and Vision Systems
Precision begins with the ability to sense and adjust to the environment. Robotic sensors and vision systems act as the robot’s “eyes,” enabling it to detect and interpret objects, spaces, and surfaces.
Advanced sensors use 3D imaging, laser guidance, and infrared detection to create a highly accurate map of the robot’s surroundings.
For instance, laser-guided sensors allow robots to detect even slight variations in position or shape, making real-time adjustments that enhance precision.
Vision systems with 3D imaging enable robots to navigate complex spaces and pick objects precisely, regardless of variations in orientation or lighting.
These sensory capabilities play a crucial role in enabling robots to adapt quickly to changing environments and complete tasks accurately.
Artificial Intelligence (AI) and Machine Learning (ML)
Artificial Intelligence and machine learning bring adaptability to robotic systems, allowing them to “learn” from previous tasks and improve accuracy over time. AI-driven robots can identify patterns, predict errors, and optimize paths to avoid obstacles or unnecessary movements.
This continuous improvement cycle is essential for complex tasks requiring flexibility and precision, such as assembling components that may have minor variations.
Collaborative Robots (Cobots) and Safety Mechanisms
Collaborative robots, or “cobots,” are designed to work safely alongside human operators, making them ideal for tasks requiring both precision and human oversight.
Cobots are equipped with sensors and force-control features that allow them to stop or adjust their movements if they encounter resistance. This capability enhances safety and allows cobots to handle delicate components that may need human adjustments in real-time.
In industries such as electronics and medical device manufacturing, cobots are invaluable for assembling small or sensitive components where both human intuition and robotic precision are essential.
Safety features like collision detection and responsive force control enable cobots to work closely with humans while maintaining accuracy.
Core Components Enhancing Robotic Accuracy
Achieving precision in robotics depends on several key components, each playing a specific role in the system’s overall accuracy. Here’s a closer look at these critical parts.
Actuators and Servomotors
Actuators and servomotors provide the power and control that enable robots to move with precision. High-quality servomotors offer fine control over movement, allowing robots to position themselves accurately and smoothly.
By adjusting torque and speed, servomotors ensure the robot can move precisely without overcompensating or wobbling, even when making tiny adjustments.
Advances in motor technology have made it possible for robots to move more quietly and efficiently, with high responsiveness to external stimuli.
This control capability is crucial for tasks that require delicate handling, such as micro-assembly in electronics or precise welding in automotive manufacturing.
End Effectors: The Importance of Grippers
End effectors are the tools attached to the end of a robotic arm, with grippers being one of the most common types used in precision tasks.
Grippers allow robots to grasp, hold, and manipulate objects with accuracy.
They come in various types, each designed to handle different materials and task requirements.
- Types of Grippers: Common gripper types include pneumatic, hydraulic, and electric grippers, each offering unique advantages. Pneumatic grippers provide a firm grip suitable for heavy materials, while electric grippers, like the Hand-E from Robotiq, allow for precision in tasks involving delicate or small objects.
- Applications for High Precision: Grippers are crucial for handling delicate components in electronics, performing precise assembly in automotive manufacturing, and working with fragile materials in the pharmaceutical industry. Adaptive grippers, like the Hand-E, offer a high degree of customization by adjusting their grip strength, angle, and sensitivity according to the object, enhancing precision and reducing the risk of errors.
- Adaptive Grippers and Flexibility: Adaptive grippers have become increasingly popular for their ability to handle complex and varying tasks. These grippers adjust in real-time, enabling robots to work efficiently even when parts differ slightly in shape, size, or material, providing the flexibility needed in fast-paced manufacturing environments.
Control Systems
Control systems monitor and adjust the robot’s movements in real-time, ensuring it maintains the highest level of precision.
These systems use data from sensors and feedback loops to keep the robot on track, even when minor adjustments are required.
Advanced control systems integrate predictive analytics and real-time monitoring, helping robots stay within micrometer tolerances in complex tasks.
For instance, in high-speed production lines, control systems prevent “drift,” ensuring that robots perform repetitive tasks with the same accuracy throughout the process.
Control systems play a critical role in managing complex, multi-step operations where even slight deviations could compromise the final product’s quality.
Conclusion
Robotic precision has revolutionized modern manufacturing, enabling companies to achieve unprecedented accuracy in complex tasks.
Through advanced sensors, adaptive grippers, and sophisticated AI, robots can meet the demands of industries where quality and consistency are paramount.
While challenges remain, continued advancements in technology are making high-precision robotics accessible and effective, promising a future where robots take manufacturing accuracy to new heights.